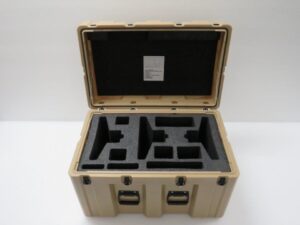
Learn more about the differences between roto-molded cases–seen here–and injection molded cases.
For most of the history of protective case packaging, roto-molded cases were the industry standard. The roto-molding process results in highly impact resistant, even wall thickness products that protect against drops, impacts and rough use. However, a new case manufacturing process soon developed: injection molding. Injection molded cases are lighter and can incorporate more complex designs. Of course, both of these manufacturing techniques offer specific advantages that may or may not work for your precise case design needs. Before engaging with Packaging Strategies Design and Technology Center of excellence to find your new case, compare the following factors that differentiate injection molded and roto-molded cases.
The Cost of the Process
The initial cost of your project may concern you before manufacturing your protective cases. Roto-molded cases are created with less expensive materials and lower pressure molding techniques, which can often translate to a slightly smaller price tag. Injection molding calls for higher pressure molding processes which, therefore, creates stronger and possibly higher-priced molds. If your case requires the fit of an injection-molded case, however, you shouldn’t always worry about the initial cost. Many times, your investment pays off as the protection your case provides means you avoid paying for equipment damage or replacements over time.
Design Complexity
Both of these case manufacturing methods can be used for various designs. Injection molding provides slightly more complex design options because of the high pressure that ensures the plastics fill every nook and cranny of the mold. The detailed and specific designs that can be created with injection molding are often quite impressive. If you don’t require a complex design, roto-molding can work well for your needs.
Production Times
Injection molding can be a surprisingly swift process because of the high pressure used. Roto-molding on the other hand, requires a little more time to mold each piece. If time concerns you, injection molded cases may be best. If you want roto-molded cases, make sure to factor in additional time so you can receive your cases when you need them.
Limited Waste
If you are concerned about the waste created during the roto-molding and injection molding processes, you are in luck! Fortunately, both methods create very limited waste during the molding process. Excess plastic, sometimes called flashing, can be removed from the product, ground up and used again in creating another case. Both processes effectively create no permanent waste, so you don’t have to worry either way.
Case Weight
Roto-molded cases contain more plastic, which often results in a heavier product. The walls of your case are often thick, especially in the corners. The thick plastic walls and insulation within them can create more weight, even though those thick walls protect your materials from all varieties of stress.
Injection molding uses less plastic, so the end product can often be 30% lighter than comparable roto-molded cases. If you are concerned about the weight of cases you will be required to carry or transport for long periods, consider injection molded cases to ease the weight you will have to transport.
The best solution for your case needs will always come down to individual factors. The experienced professionals at the Packaging Strategies Design and Technology Center can help you determine which case best suits your needs.
DEPEND ON PACKAGING STRATEGIES FOR YOUR CUSTOM PACKAGING NEEDS
Packaging Strategies has assembled a team with over 80 years of experience in design, engineering, development, manufacturing, and sales. We created the Packaging Strategies Design and Technology Center to create and manufacture complete systems integration packages and container solutions of all sizes and materials for our clientele. Many of these clients are federal agencies or in the private sector. No matter what you need to carry, Packaging Strategies is sure to have the right case for the job. You can view our website here, and follow us on Facebook, Twitter, Flickr, and Linkedin.